The number of passengers and aircraft movements at Indonesia’s Soekarno-Hatta International Airport in Jakarta has been increasing dynamically for years, prompting continuous modernisation and expansion of the infrastructure. Most recently, one of the three runways was due for rehabilitation. However, work could only be carried out between 11 pm and 5 am, when no planes were taking off or landing on the runway – making the task all the more challenging.
For the paving work on this runway, which measures 3.6 km long and 60 m wide, PT Roadmixindo Raya relied on two Super 1880 L pavers from Vögele. The machines worked alongside each other and paved four layers each ‘hot-to-hot’ at a working width of 8 m – two base layers with a thickness of 7-8 cm each, an approximately 8 cm thick binder course and a 2 cm surface layer.
Strict requirements
The paving quality requirements were quite strict for this project. At international airports, paving requirements are based on the strict regulations of two aviation authorities, namely the International Civil Aviation Organisation (ICAO) and the Federal Aviation Administration (FAA). They define a variety of parameters ranging from the mix quality and tensile strength to the surface quality and paving precision. Equally strict requirements apply to the formation of joints.
Besides having to comply with the strict quality requirements, care also had to be taken to ensure that sufficient mix of the required quality was supplied and used. Thanks to their large material hopper, excellent laydown rate, powerful performance and robustness, the Vögele Super 1880 L pavers were ideal for the job. They paved together ‘hot to hot’ in a slightly staggered formation – a paving method that ensures particularly dense and stable bonding of the individual courses and provides long-term protection against the penetration of water.
The Super 1880 L pavers are equipped with a six-cylinder diesel engine featuring a rated power output of 158 kW. The paver operators were able to run the engine in Eco mode when the job required less power. In this mode, the nominal engine speed is reduced from 2,000 rpm to 1,700 rpm, which leads to a reduction of the operating costs and noise emission levels.
Maximum productivity was another crucial factor on the airport construction site. “To make the best use of the working hours, the processes had to run smoothly. This was the only way we could keep to the schedule,” said Tadjus Tamsil, director at PT Roadmixindo Raya, the contractor on the project.
One of the highlights of these Vögele pavers, according to Mr Tamsil, is the large material hopper with a capacity of 15 t. Its considerable length and low material feed height allowed each tipper truck to easily dock with the Super 1880 L and quickly offload the mix. “This meant that the trucks were able to quickly transfer their loads of mix, enabling us to maintain a high laydown rate and work continuously without interruption,” he said.
Andrew Davian, project manager at PT Roadmixindo Raya, added, “The fact that the Super 1880 L also made it easy to meet the required criteria for surface quality and paving precision was an enormous relief for the paving crew during the demanding work through the night.”
The AB 500 TV extending screeds used on the project also played an important role in ensuring the high paving quality. The AB 500 has a basic width of 2.55 m and can be hydraulically extended to a width of 5.00 m. With bolt-on extensions, it can pave widths of up to 8.5 m.
“Maximum quality and perfect grade and slope control are particularly critical on a project like here at the airport. The combination of the AB 500 and the tamper bar and vibration compaction systems enabled us to achieve outstanding pre-compaction and, consequently, a very high-quality result,” said David Gouw Tama Priatna, director at PT Roadmixindo Raya.
In addition, the extending screed reached the specified temperature quickly and evenly thanks to the electric screed heating system. This consistently heats all components that come into contact with the asphalt mix and allows a homogeneous surface structure.
The intuitive ErgoBasic operating concept helped deliver precise paving results. It was developed on the basis of Vögele’s ErgoPlus operating system with the aim of being just as quick, precise and intuitive – but slimmed down to the most important paving functions.
Vögele has also developed a system for automated grade and slope control to complement the ErgoBasic operating system, namely Niveltronic Basic. This system is fully integrated into the machine control system and therefore tailored precisely to suit the Super 1880 L.
“ErgoBasic is a major plus point of the Vögele paver. The operating concept enables quick and simple control and makes it easier for the paving crew to achieve precise results,” said Faisol Fuad, director at PT Roadmixindo Raya.
This south runway rehabilitation project is expected to be completed by end of August 2025.
Note: This story has also been published in the Jul/Aug 2025 issue of SEAC. Click here to read it online or here to download the PDF file (pages 32-34).
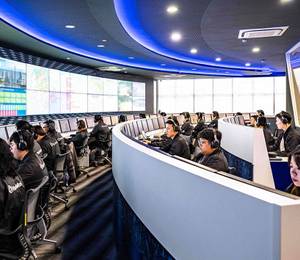
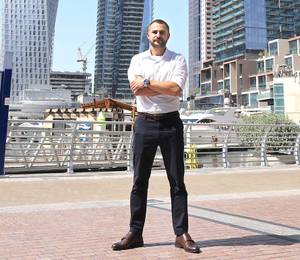
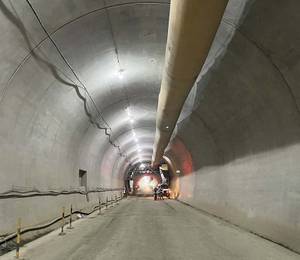
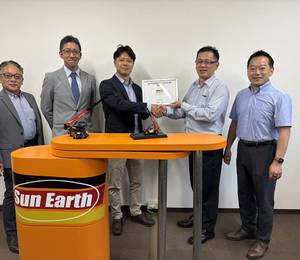

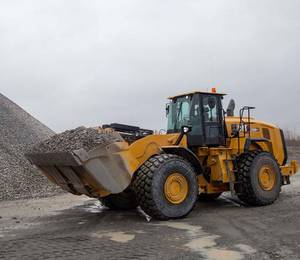

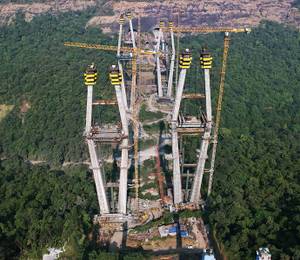
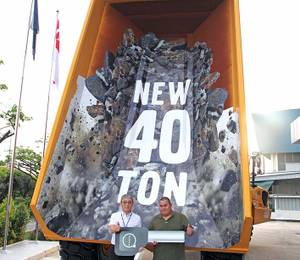
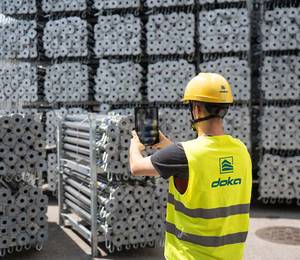