Global manufacturer ULMA Construction offers comprehensive formwork and scaffolding solutions for the construction industry. The products are used in a wide range of applications, including building, civil engineering, industrial and restoration projects.
Based in Oñati, Spain, ULMA was established in 1961 by six partners: Pedro Ugarte, Esteban Lizarralde, Julián Lizarralde, Isidro Mendiola, Ignacio Maiztegui and Julián Ayastui. The company’s name was derived from the initials of the founders’ surnames.
In 1963, ULMA introduced its first scaffolding system ‘JJEIP’ and took the first steps in the construction industry. The company began its internationalisation process in 1976.
Today, ULMA is present in more than 50 countries, with more than 20 subsidiaries all over the world. The company employs about 2,168 people globally.
Comprehensive solutions
Catering for all types of concrete structures, ULMA systems comprise wall, column and slab formwork, shoring systems, high-tech climbing formwork, timber beams and plywood, tunnel and bridge formwork and a wide range of safety equipment.
Among the highlights is the MK system, shared Edward De Marta, ULMA head of sales for East Asia and Pacific. “It is very versatile and can be adapted to a large number of applications. This makes the system an attractive choice for our customers.”
Speaking to SEAC at a recent press event, Mr De Marta said the self-climbing formwork is also an important solution. This system can be lifted hydraulically without the need for a crane and is highly cost-effective due to shorter construction cycles.
The self-climbing, guided and conventional climbing formwork systems are most appropriate for high walls. They are typically used in the construction of towers, skyscrapers, cores, bridge piers, pylons and dams. These climbing systems are compatible with all types of ULMA wall formwork.
The wall and column formwork is well suited for the construction of concrete walls, columns, side walls, foundations, footings, abutments, etc. The slab formwork covers various applications, such as large slabs, solid and lightened, inclined surfaces, hanging beams, infilling, column heads, cantilevers, etc.
ULMA also manufactures tunnel formwork – specialising in cut-and-cover and mine tunnel construction methods – and bridge formwork for the construction and repair of different types of bridges.
The company’s high load-bearing prop and shoring systems are designed for the construction of slabs, bridge decks, column heads, tunnel vaults or any other structure requiring the use of shoring.
In addition, ULMA BRIO Ringlock multidirectional scaffolding is ideal for the construction, industrial, energy, naval and entertainment industries. It is extremely flexible, safe and cost-effective, allowing high assembly rates due to its design and simplicity. The company also offers frame scaffolding, suitable for all types of facade covering works for restoration, renovation, etc.
Southeast Asian presence
ULMA has established itself in the Southeast Asian market, working on many major projects across the region. “In general, Southeast Asia is a growing market for us – like Vietnam, Indonesia and the Philippines – which presents a lot of opportunities,” said Mr De Marta.
“The Cebu-Cordova Link Expressway (CCLEX) in the Philippines, for example, is one of our major projects.” For this cable-stayed bridge, which was opened in 2022, ULMA undertook the most technically challenging structures: the pylons, the working platforms for installation of the cable-stayed structure, as well as the piers, pier caps, and pier segments. The company’s ATR system provided a solution for the octagonal pylons of 150 m in height with variable sections.
“Our work on the CCLEX project was a big success; it serves as an excellent reference for us not just in Asia, but around the world,” said Mr De Marta. The company is now involved in more key infrastructure projects in the Philippines, such as the Malolos-Clark Railway (Package 2 and 4) and the Davao City Bypass, as well as a variety of residential, office and mixed-use development projects.
In Indonesia, ULMA also provided its solutions for the construction of Jakarta-Cikampek II Toll Road, added Mr De Marta. This essential road (about 38 km) is part of a government masterplan to ease traffic congestion towards and around Jakarta and to boost economic growth by improving the country’s infrastructure.
Other major projects that ULMA has taken part in include: the Thamrin Nine Tower 1, Indonesia’s tallest building at over 330 m high; Ulu Jelai Hydroelectric Project and Tanjung Bin Power Plant, Malaysia; VietinBank Business Centre Office Tower in Hanoi, Vietnam; Marina Bay Cruise Centre Singapore plus various residential, retail, office, industrial and MRT projects, Singapore; to name just a few.
Note: SEAC visited ULMA’s facility in June 2024, as part of a press event organised by ANMOPYC in collaboration with ICEX (the Spanish Institute for Foreign Trade). This story has also been published in the Nov/Dec 2024 issue of SEAC (with more images). Click here to read it online or here to download the PDF file, on pages 44-45.
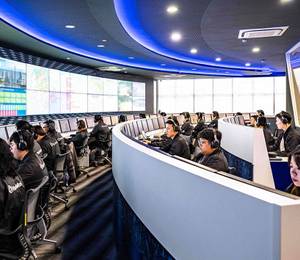
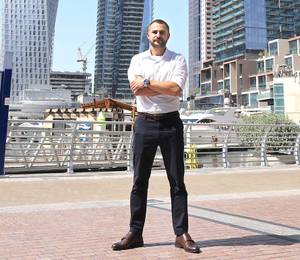
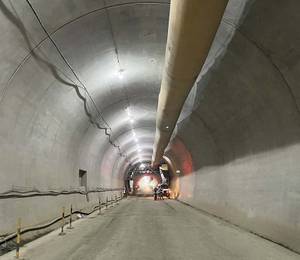
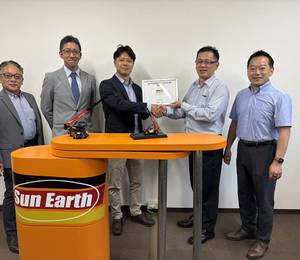

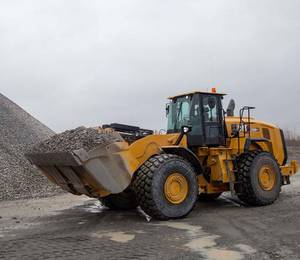

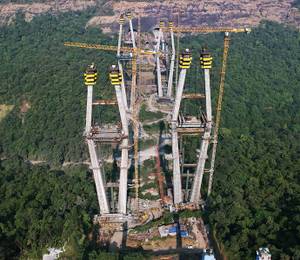
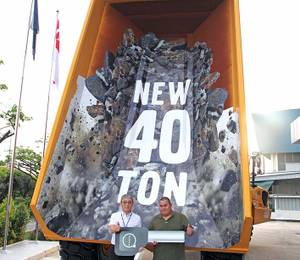
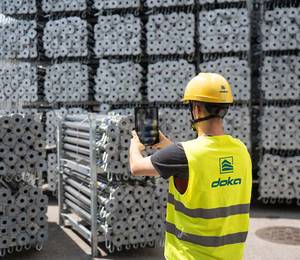