During a press event at tower crane manufacturer Jaso’s facility in Idiazabal, Spain, the global trade media had an opportunity to see first-hand the company’s new luffing model, the J638PA. This unit has been introduced to worldwide markets, including Asia.
The J638PA features a maximum reach of 65 m, providing greater flexibility and access to heights. With a maximum load capacity of 32 t and a maximum tip load of 7.2 t at its full reach, this tower crane has been built to handle the most demanding projects with ease.
Speaking to SEAC at the press event, Jaso said the J638PA is highly suitable for the Asian market. The crane is also designed with a strong focus on environmental responsibility. Its efficient operation and sustainable features align with the company’s commitment to minimising environmental impact while maximising productivity.
In addition, the J638PA is equipped with Jaso’s Optimus Line technology (including Eco Mode, Safety Pack, Smartlink, Extra Lift, Opti Cube, TC Diagnose System, and more) to ensure optimal performance, efficiency and safety, making the crane ideal for construction projects of all scales.
“Addressing technical, commercial, construction, logistical, safety and environmental considerations, this crane stands as a versatile, sustainable and technologically advanced solution,” said Jaso.
High-capacity cranes for Asia
Talking about its presence in Asia, Jaso shared that it is currently active in Singapore, Hong Kong, South Korea and Taiwan, with some projects in the Philippines. The company is also open to explore other markets in the region.
Jaso’s cranes have been involved in various residential projects and high-rise developments, especially those using PBU (prefabricated bathroom unit) and PPVC (prefabricated prefinished volumetric construction).
The growing trend towards PPVC projects, particularly in Asia, has led to increased demand for cranes with high lifting capacities, explained Jaso. As a response, the company developed the J1400 model.
A number of Jaso J1400 tower cranes have recently been deployed on a residential project in Singapore, which was built using the PPVC method. The cranes were used to lift heavy materials, such as PPVC modules weighing up to 35 t.
With a maximum 80-m-long jib, the J1400 can lift a maximum load of 64 t and has a tip load of 10.5 t. At 40 m reach, the crane’s capacity is still 36 t. Increasing the hook height to 150 m only reduces the capacity by 1.4 t to 34.6 t, despite the extra 28-mm steel wire rope weight, said Jaso.
The J1400’s counter-swing radius is 29 m when using 80 m boom, and 18.1 m with 40 m boom. With steel counterweights, it can be reduced by a further 1.8 m. The crane’s tower system is in 5.6-m-long sections with a 2.16 x 2.16 m footprint. The hoist mechanism is 110 kW or 132 kW, and for greater safety, a secondary clamp brake is available on hoist and trolley.
Jaso added that the full crane, including the top kit, can be transported in standard 40-ft ISO shipping containers with no special flat rack or open top needed. This is facilitated by a folding counter jib design.
The mast sections, slewing table, and jacking cage are all small in size, making them easy to transport to the jobsite. During erection, there is no need to use large mobile or crawler cranes as the heaviest component of the J1400 is only 21,600 kg, which can be reduced to around 10 t if required.
Jaso further pointed out the key benefits of using PPVC and PBU in construction:
-
Higher efficiency. The pre-assembly of volumetric units can be carried out off-site, in tandem with other activities on-site. These off-site works at the ground level can minimise the wastage of materials, and reduce the need to hoist raw materials onto elevated blocks under construction.
-
Reduced need for manpower on-site and improved site safety. By fabricating the volumetric modular units off-site in a controlled factory environment, fewer workers are required on-site, thereby improving overall site safety.
-
Minimised environmental impact. With part of the finishes done off-site, less noise and dust is generated at construction sites, thereby minimising disamenities to surrounding residents. It also helps to improve housekeeping at construction sites.
-
Better construction quality. Volumetric construction in a factory environment offers more uniform and better quality workmanship. The incidence of wet construction joints is also reduced, thereby improving the water tightness of wet areas.
Note: SEAC visited Jaso’s facility in June 2024, as part of a press event organised by ANMOPYC in collaboration with ICEX (the Spanish Institute for Foreign Trade). This story has also been published in the Sept/Oct 2024 issue of SEAC. Click here to read it online or here to download the PDF file, on pages 54-55.
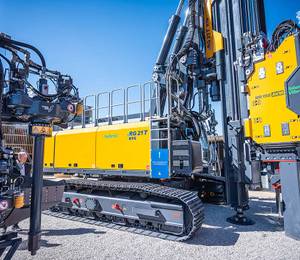
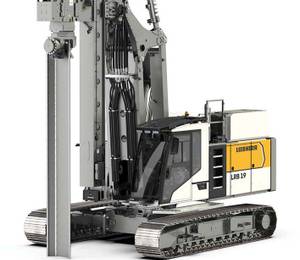
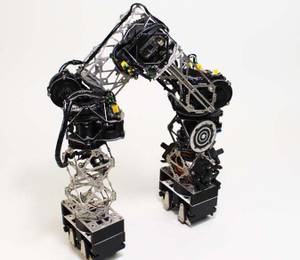
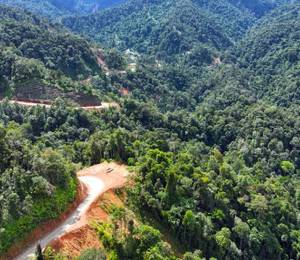
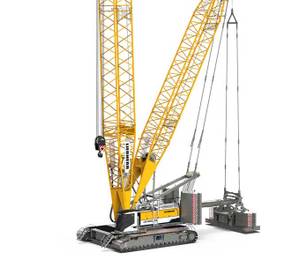
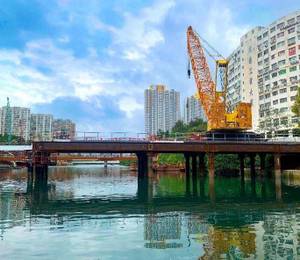
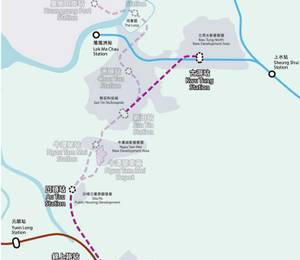